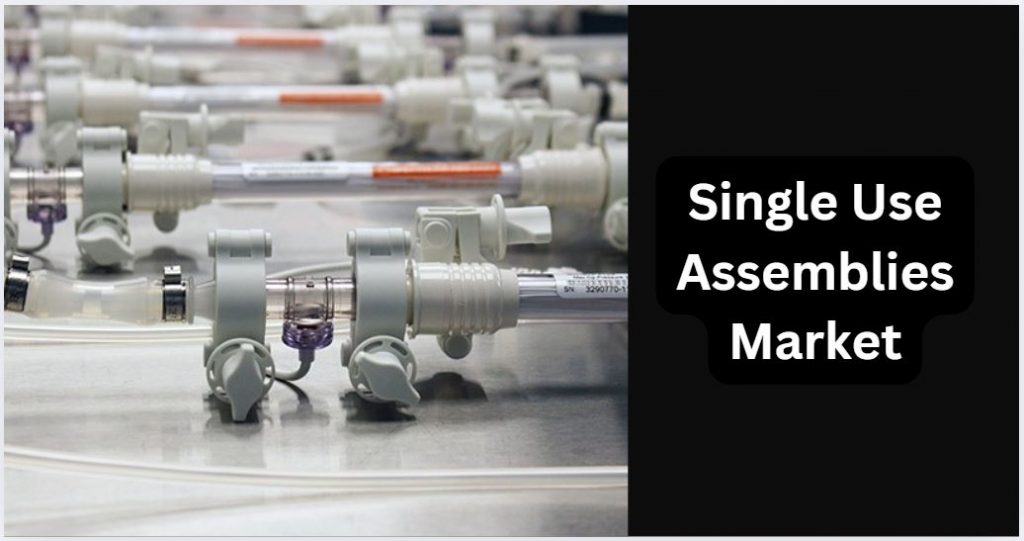
Market Overview
The global Single Use Assemblies Market was valued at USD 2,480.91 million in 2023 and is anticipated to reach USD 6,991.12 million by 2032, expanding at a CAGR of 12.2% during the forecast period (2023–2032). This growth is driven by increasing demand in the biopharmaceutical industry for scalable, contamination-free, and time-efficient solutions. Single use assemblies (SUAs) offer a critical advantage in minimizing cleaning requirements, lowering validation costs, and enhancing operational flexibility.
As the global healthcare industry undergoes rapid transformation, biopharmaceutical manufacturers are leaning towards more agile and disposable systems. The shift from traditional stainless-steel systems to single use technologies reflects the market’s increasing need for faster production cycles and reduced downtime. This evolution is particularly vital amid rising demand for personalized medicine and small batch production.
The COVID-19 pandemic accelerated the adoption of SUAs, demonstrating their capability to support scalable vaccine and biologic production under high-demand conditions. Furthermore, growing research into cell and gene therapy applications is amplifying the relevance of SUAs. Their role in aseptic fluid transfer, filtration, and formulation further contributes to market expansion.
Overall, the market is poised for robust growth, driven by regulatory support, continuous innovation, and expanding global biopharmaceutical infrastructure. As the industry pursues cost-effective and risk-reducing technologies, single use assemblies are set to play an integral role in next-generation manufacturing.
Download Sample Report: https://www.credenceresearch.com/report/single-use-assemblies-market
Market Drivers
Increasing Biopharmaceutical Production
The global increase in biologics manufacturing is one of the core drivers for SUAs. With rising demand for monoclonal antibodies, vaccines, and cell therapies, manufacturers are adopting flexible, scalable, and contamination-free production processes. Single use assemblies reduce cleaning and validation time, making them ideal for frequent product changeovers. Their implementation enables facilities to scale operations quickly without disrupting workflows. Additionally, single use systems support continuous manufacturing, reducing batch-to-batch variability. This shift has helped shorten production cycles while maintaining high-quality standards. Biopharma leaders are investing in modular facilities that heavily rely on single use systems, solidifying their role in modern drug manufacturing.
Shift Towards Personalized Medicine
As medicine becomes increasingly patient-specific, batch sizes are shrinking. This evolution necessitates more adaptable manufacturing setups, which SUAs are well-suited for. Their modularity allows rapid customization without compromising sterility or efficiency, addressing the need for quick response in small-scale therapeutic development. Personalized treatments like gene therapies and orphan drugs require flexible, small-batch production. SUAs support quick product transitions with minimal downtime, making them indispensable in personalized healthcare. Additionally, single use systems can be reconfigured quickly for multiple applications. This adaptability aligns with the goals of precision medicine and innovation in clinical-stage drug development.
Reduced Risk of Cross-Contamination
Traditional stainless-steel systems pose a higher risk of product contamination between batches. Single use systems eliminate this by providing pre-sterilized components that are used once and discarded. This reduces human error, enhances product purity, and aligns with stringent GMP compliance in regulated environments. With fewer cleaning requirements, facilities reduce chemical use and water consumption. This also lowers the risk of contamination from cleaning agents. In aseptic manufacturing environments, SUAs provide superior sterility assurance levels. Regulatory bodies increasingly favor facilities using SUAs due to their high compliance rates and safety profiles. As sterility demands grow, the reliance on SUAs becomes more prominent.
Cost Efficiency in Manufacturing
While the initial investment in SUAs can be higher, the overall lifecycle cost is significantly lower. Companies save on cleaning, sterilization, validation, and labor costs. Additionally, time saved on setup and downtime between batches enables faster turnaround and improved production throughput, making it an economically attractive choice. Reduced infrastructure needs lower facility overhead costs, especially in small-scale production. Manufacturers benefit from simplified supply chains and predictable operational budgets. Shorter production cycles mean faster time-to-market, which can be critical in competitive biotech sectors. As companies prioritize lean operations, SUAs emerge as a cost-effective and scalable alternative to traditional setups.
Market Challenges
High Upfront Costs
One of the major challenges is the significant upfront investment required for implementing SUAs. While they save costs long-term, initial expenditure on new systems, validation, and staff training can deter small and mid-sized enterprises from early adoption. These costs also include process redesign and facility adaptation. For startups, securing sufficient capital for SUAs may delay go-to-market strategies. The absence of immediate returns discourages risk-averse firms. This financial burden often restricts adoption to larger firms with long-term strategic investments in biomanufacturing. Addressing this barrier requires increased awareness of ROI timelines and financing options for smaller players.
Limited Standardization
A lack of standardization across manufacturers leads to compatibility issues. Differences in component design and material standards can hinder integration and scalability. This poses a problem for companies seeking seamless, plug-and-play production setups using multiple vendors. Inconsistent regulatory interpretations across regions further complicate harmonization. Without universal protocols, system validation becomes more complex and time-consuming. Interoperability concerns limit supply chain flexibility and increase dependency on specific brands. These challenges underscore the need for industry-wide collaboration and the development of shared specifications that ensure consistency and quality.
Environmental Concerns
The disposable nature of SUAs generates substantial plastic waste, raising concerns about environmental sustainability. While many manufacturers are exploring recyclable or biodegradable options, widespread eco-friendly solutions are still under development, potentially limiting adoption in sustainability-focused regions. Regulatory and consumer pressures are prompting companies to consider greener practices. However, the trade-off between performance and sustainability remains a challenge. Waste disposal compliance adds cost and complexity to operations. Without clear disposal regulations and recycling infrastructure, sustainability goals remain difficult to achieve. As environmental scrutiny intensifies, sustainable innovation becomes a decisive factor for long-term growth.
Supply Chain Disruptions
The market relies heavily on a few key suppliers for critical components. During global events like the COVID-19 pandemic, supply chain constraints caused production delays. Dependency on specific vendors or geographies increases vulnerability and may affect business continuity planning. Lead times for single use components can stretch production timelines and limit flexibility. Any disruption in raw material sourcing or transportation affects delivery schedules. This has driven demand for dual sourcing and regionalized supply chains. To address this, companies must build more resilient procurement strategies and collaborate closely with trusted suppliers to avoid operational setbacks.
Market Opportunity
Expanding Role of CMOs & CROs
Contract Manufacturing Organizations (CMOs) and Contract Research Organizations (CROs) are increasingly integrating SUAs to offer cost-efficient and flexible services. Their expanding footprint globally creates opportunities for SUA vendors to provide customizable and scalable systems tailored to evolving client needs. As CMOs handle a growing share of biologics production, SUAs support rapid turnaround and regulatory compliance. These organizations value process repeatability and quality assurance, areas where SUAs excel. Vendors offering pre-validated, plug-and-play solutions gain a competitive edge. The scalability of SUAs aligns perfectly with the dynamic project pipelines handled by outsourcing partners.
Rising Investments in Cell & Gene Therapy
The cell and gene therapy segment demands ultra-clean environments and modular processing systems. SUAs play a pivotal role in these settings by reducing contamination risks and streamlining formulation and filling processes. This trend opens avenues for specialized product innovations and application-specific solutions. Regulatory focus on sterility and patient safety drives SUA adoption in advanced therapies. Custom-configured systems reduce turnaround time for highly targeted treatments. As more cell therapy pipelines move toward commercialization, the demand for efficient and reproducible manufacturing tools like SUAs continues to grow, presenting a massive growth window.
Advancements in Material Science
Emerging material technologies offer better compatibility, durability, and sustainability for SUAs. Innovations in polymers and barrier films can address sterility, leachability, and environmental issues, making the product category more robust and appealing to hesitant buyers. New materials enhance chemical resistance and product stability. Manufacturers can now produce assemblies with extended shelf lives and broader application ranges. These improvements lower regulatory risk and enhance user confidence. Continued R&D investment in polymer engineering will shape the next generation of SUAs, pushing the industry toward safer and more versatile products.
Growth in Emerging Markets
Emerging economies, especially in Asia-Pacific and Latin America, are expanding their biopharmaceutical manufacturing capacities. As infrastructure improves and regulatory frameworks evolve, the demand for affordable, efficient, and compliant single use systems is expected to surge, opening up lucrative regional markets. Government initiatives are incentivizing local production, further boosting SUA demand. Training programs and regulatory harmonization are addressing adoption barriers. Lower operational costs in these regions make them attractive hubs for global outsourcing. As companies shift focus to high-growth territories, SUAs will be critical in scaling compliant manufacturing infrastructure efficiently.
Market Segmentation
By Product Segment:
- Bag Assemblies
- Filtration Assemblies
- Bottle Assemblies
- Tubing Assemblies
- Others
By Solution Segment:
- Standard Solutions
- Customized Solutions
By Applications Segment:
- Cell Culture & Mixing
- Filtration & Purifications
- Storage Applications
- Formulation and Fill-Finish Application
- Others
By End-User Segment:
- Pharmaceutical & Biopharmaceutical Companies
- Contract Research & Contract Manufacturing Organizations
- Academics & Research Institutes
By Region
North America
- U.S.
- Canada
- Mexico
Europe
- Germany
- France
- U.K.
- Italy
- Spain
- Rest of Europe
Asia-Pacific
- China
- Japan
- India
- South Korea
- Southeast Asia
- Rest of Asia-Pacific
Latin America
- Brazil
- Argentina
- Rest of Latin America
Middle East & Africa
- GCC Countries
- South Africa
- Rest of the Middle East and Africa
Regional Analysis
North America
North America dominates the SUA market due to its advanced healthcare infrastructure and large-scale biologics manufacturing. The U.S. leads regional demand, driven by rapid technological adoption and regulatory support. Growth is supported by strong investments in R&D and expansion of CDMOs. The region is home to several top pharmaceutical firms with high adoption rates of disposable systems. The focus on innovation and rapid drug development continues to drive demand. Canada and Mexico are also showing steady progress, especially in contract manufacturing and academic research.
Europe
Europe follows closely, with countries like Germany, France, and the U.K. investing in biopharmaceutical innovation. EU regulatory frameworks are encouraging adoption of disposable technologies to meet stringent GMP guidelines. Growing adoption of cell therapy further supports market growth. The region’s strong focus on sustainable manufacturing also pushes development of eco-friendly SUA materials. Italy and Spain are seeing significant expansion in their biotech sectors. Rest of Europe is catching up, aided by supportive policies and rising health awareness. The diversity of pharmaceutical firms across Europe ensures broad SUA application.
Asia Pacific
Asia Pacific is expected to witness the fastest growth. China and India are scaling biomanufacturing capabilities, driven by government support and growing local demand. Japan and South Korea contribute with high-tech innovation and increasing clinical trials requiring flexible manufacturing. The region’s cost advantage and skilled labor make it attractive for global firms. South-East Asia is emerging as a new hub for biologics manufacturing. Investments in industrial parks and science zones are increasing. Local manufacturers are also embracing SUAs for export-quality production.
Latin America
Brazil and Argentina lead SUA adoption in Latin America, as pharmaceutical exports rise. Improvements in regulatory structures and increased foreign direct investment are pushing demand for compliant manufacturing systems like SUAs. The region benefits from growing partnerships with North American pharma companies. Domestic firms are expanding production lines for biologics and generics. Rest of Latin America is showing gradual uptake, aided by government incentives and healthcare reforms. Challenges around logistics persist but are being actively addressed. Overall, the outlook remains promising with targeted investments.
Middle East & Africa
GCC countries are investing in biotech and pharmaceutical manufacturing under national healthcare transformation plans. In Africa, South Africa is emerging as a key market, with growing awareness and government initiatives supporting modernized production environments. These regions are focusing on building resilient healthcare infrastructure post-COVID-19. International collaborations are helping transfer technology and expertise. Regulatory agencies are working toward harmonized standards. Though the market is in its early stages, the potential for expansion is strong. Local production of vaccines and essential drugs is a top policy priority driving SUA demand.
Top Companies in the Market
- Thermo Fisher Scientific Inc.
- Sartorius AG
- Danaher Corporation
- Merck KGaA
- Avantor, Inc.
- Parker-Hannifin Corporation
- Saint-Gobain S.A.
- Repligen Corporation
- Corning Incorporated
- Entegris
Future Outlook
- The single use assemblies (SUA) market is expected to witness sustained growth driven by increasing demand for biologics, vaccines, and personalized therapies. Manufacturers will continue to prioritize flexibility, sterility, and cost efficiency, propelling further adoption of SUAs across global facilities.
- Rising adoption of continuous bioprocessing will create demand for integrated SUAs that streamline operations and improve yield in real-time production environments. This trend will shape the future of efficient drug manufacturing practices.
- Miniaturization and automation of manufacturing processes will drive innovation in compact and smart SUAs. These systems will enable real-time monitoring and adaptive control, enhancing overall process performance.
- Growth in personalized medicine will spur demand for single-use solutions tailored for small-batch and highly specialized therapies. This will enhance responsiveness and production efficiency in niche treatment areas.
- Biopharma expansions in Asia-Pacific and Latin America will open up new revenue streams for SUA vendors. This growth will be supported by improving infrastructure and local production incentives.
- Integration of sensors and smart materials in SUAs will enable predictive maintenance. These advancements will also enhance process analytics, ensuring higher compliance with GMP standards.
- Sustainability will become a central innovation focus, with companies investing in recyclable and biodegradable components. These developments will address environmental concerns and regulatory pressures.
- Increased collaboration between SUA manufacturers and biopharma companies will foster customized system development. This will accelerate drug production cycles and reduce time-to-market.
- Digital twin technologies may influence future SUAs, offering simulation-based process optimization. This will support faster scale-up and efficient decision-making in production design.
- Emerging fields like mRNA vaccines and gene editing will drive specialized demands for sterile, rapid-deployment single-use solutions. These systems will support scalability and innovation in cutting-edge therapeutic research.
Download Sample Report: https://www.credenceresearch.com/report/single-use-assemblies-market