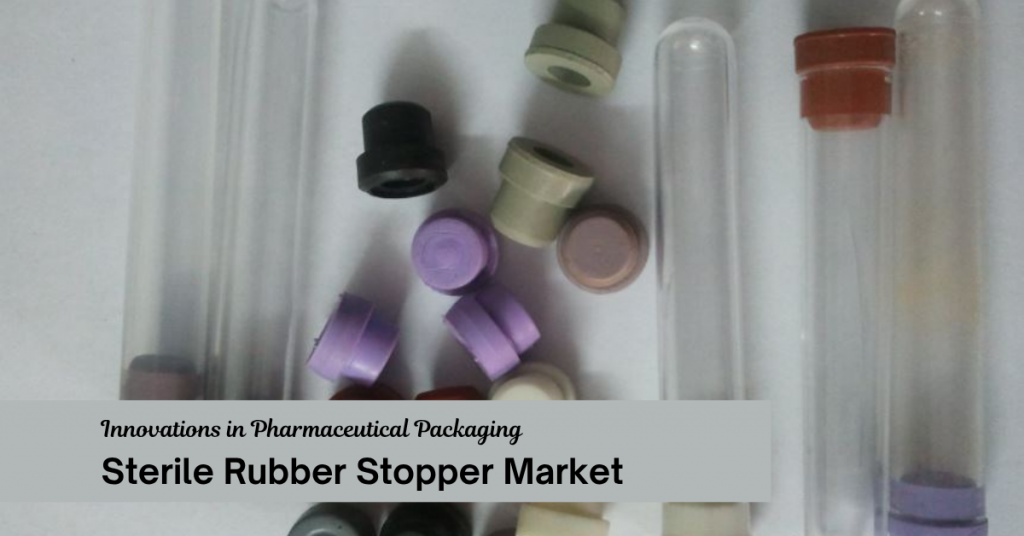
Market Overview
The sterile rubber stopper market is projected to grow from USD 2,675 million in 2024 to USD 4,199.6 million by 2032, registering a compound annual growth rate (CAGR) of 5.80% during the forecast period. This steady expansion highlights the growing importance of sterile packaging components in the global pharmaceutical and healthcare industries. As the demand for injectable drugs, vaccines, and biologics increases, so does the need for reliable and contamination-free sealing solutions.
Sterile rubber stoppers play a pivotal role in ensuring the integrity of parenteral packaging. They are used extensively to seal vials, preventing microbial contamination, maintaining drug stability, and extending product shelf life. This critical function places sterile rubber stoppers at the center of pharmaceutical packaging operations worldwide. Given the growing regulatory scrutiny and emphasis on safety, manufacturers are adopting advanced sterilization and coating techniques to meet stringent quality standards.
In the current global context, where vaccine production, biologics development, and personalized medicines are witnessing heightened focus, the sterile rubber stopper market has gained unprecedented relevance. Moreover, increased investments in R&D and biotechnology infrastructure are supporting long-term growth. The demand surge is further amplified by the expansion of clinical trials and the development of new therapies across emerging economies. Together, these factors contribute to a dynamic and resilient market poised for sustained growth over the next decade.
Read more: https://www.credenceresearch.com/report/sterile-rubber-stopper-market
Market Drivers
Rising Demand for Injectable Drugs
The growing prevalence of chronic conditions such as diabetes, cancer, and autoimmune diseases has led to a surge in injectable therapeutics. These medications require sterile packaging to ensure efficacy and safety. Rubber stoppers offer a secure seal for injectable vials, making them indispensable in hospital and clinical settings. The convenience and fast action of injectable drugs over oral alternatives make them a preferred choice for both acute and chronic conditions. Hospitals and diagnostic centers are also stocking higher volumes of injectables, thus increasing demand for safe and sterile closures. Moreover, parenteral administration bypasses the digestive system, making it ideal for patients with compromised gastrointestinal function. Consequently, demand for sterile rubber stoppers continues to grow in parallel with injectable drug utilization. Additionally, governments globally are scaling up vaccination and treatment programs that rely heavily on injectable drugs.
Expansion of Biopharmaceuticals and Vaccines
The biopharmaceutical sector has been expanding rapidly, driven by increased R&D and innovation. Vaccines and biologics are sensitive to contamination and require high-quality closures. Sterile rubber stoppers ensure compatibility and integrity, supporting the safe storage and administration of these life-saving treatments. The growth of monoclonal antibodies, cell therapies, and gene therapies adds further momentum to the market. These therapies demand enhanced compatibility with packaging components. Moreover, the post-pandemic focus on global immunization efforts has led to higher production volumes for vaccines, thereby generating higher consumption of sterile stoppers. As more biotech companies enter the market, demand for specialized stoppers tailored to biologics is also increasing. The rise of mRNA technologies also necessitates advanced stopper performance to preserve molecular stability.
Stringent Regulatory Standards
International regulatory agencies such as the FDA and EMA have enforced strict guidelines on pharmaceutical packaging. Sterile rubber stoppers must comply with safety, sterility, and material compatibility standards. This regulatory push compels manufacturers to adopt advanced materials and sterilization technologies, driving market growth. Regulatory audits often scrutinize every aspect of packaging, including interaction between drug and closure. Manufacturers must document their processes and demonstrate product stability over shelf life. Moreover, approval delays due to packaging non-compliance have serious commercial consequences, compelling manufacturers to prioritize high-quality stopper solutions. This is pushing the industry towards standardization and validation of materials and processes. Furthermore, companies that demonstrate compliance are more likely to gain market access and win trust from major pharmaceutical clients.
Technological Advancements in Material and Coating
Innovations in rubber formulations, such as bromobutyl and chlorobutyl, have enhanced chemical resistance and reduced extractables. Additionally, coatings like Flurotech and B2 Coating have improved the performance of stoppers by minimizing drug interactions. These advancements boost the reliability of sterile rubber stoppers, encouraging wider adoption. For instance, newer coatings can prevent leaching of compounds and reduce particle generation inside vials. The evolution of elastomeric materials allows better performance in extreme storage conditions such as freezing or lyophilization. Additionally, precision molding and micro-cleaning processes have enhanced consistency across production batches. These innovations align with pharmaceutical industry goals of improving drug safety and regulatory compliance. Manufacturers are also exploring hybrid materials that combine barrier protection with user-friendly design.
Market Challenges
High Manufacturing Costs
Producing sterile rubber stoppers involves multiple stages, including molding, sterilization, and quality assurance. Advanced materials and coating technologies raise production expenses, limiting affordability for small-scale manufacturers. The need for ISO-certified facilities and cleanroom environments further escalates capital investment. As the industry moves toward more sophisticated stopper designs, production complexities and validation procedures also increase. For small and mid-sized players, these cost structures can become a barrier to market entry and long-term sustainability. Cost inefficiencies also impact profit margins and pricing competitiveness in developing economies.
Stringent Quality Control Requirements
Maintaining high sterility standards necessitates cleanroom facilities and advanced testing equipment. Quality assurance protocols are rigorous, and failure to comply can lead to recalls or regulatory penalties, posing a challenge to market players. Testing for microbial contamination, leachables, extractables, and physical properties requires significant technical expertise and infrastructure. Any deviation in standards can compromise drug safety and tarnish the brand’s reputation. These strict standards, though necessary, add operational and financial pressures. Many small-scale suppliers often struggle to meet GMP and ISO standards consistently.
Raw Material Volatility
The price and availability of raw materials such as synthetic rubber compounds are influenced by global supply chains. Disruptions in raw material procurement can affect production schedules and pricing. Political instability, trade barriers, and natural disasters can affect key raw material suppliers. Volatile pricing also affects forecasting and inventory management. To mitigate risks, manufacturers must diversify suppliers or invest in material substitution research, which increases complexity. These fluctuations also hinder long-term planning and contractual agreements with end users.
Intense Market Competition
Several players operate in this market, offering similar product lines. Differentiation becomes challenging, leading to price wars and reduced margins. Established companies with large-scale capabilities tend to dominate, creating entry barriers for new entrants. Continuous innovation is necessary to maintain market relevance, but not all players can afford the R&D investment. Furthermore, brand loyalty in the pharmaceutical industry often rests on long-term supplier relationships, making it hard for newer brands to penetrate large accounts. The commoditization of basic stopper types further intensifies the competition.
Market Opportunity
Emerging Markets Adoption
Emerging economies such as India, Brazil, and Vietnam are witnessing increased pharmaceutical production and regulatory improvements. These regions represent untapped potential for sterile rubber stopper manufacturers looking to expand their footprint. As governments improve public healthcare systems and enforce stricter drug safety norms, demand for compliant packaging solutions is expected to grow. Local manufacturing units are also seeking reliable suppliers to reduce import dependencies. Foreign investments in local pharmaceutical ventures are further opening doors for packaging material providers.
Personalized Medicine and Niche Drugs
The rise of personalized and small-batch medicines demands packaging solutions that support limited production runs with high reliability. Sterile rubber stoppers are well-suited for such applications, offering opportunities for customization. Small pharmaceutical startups and specialty drug developers require closures tailored to their unique formulations. Offering custom-size and low-volume batches of high-quality stoppers could open niche but profitable markets for innovative suppliers. This trend also facilitates the entry of boutique packaging manufacturers into premium segments.
Green and Sustainable Initiatives
Growing awareness around sustainability is pushing manufacturers to develop eco-friendly stoppers. Biodegradable rubber materials and sustainable coatings can open new market segments and fulfill environmental compliance goals. The move toward green chemistry and carbon-neutral production lines is not only environmentally responsible but also commercially strategic. Companies adopting sustainable practices may benefit from government incentives and consumer goodwill. Long-term contracts with green-certified suppliers may soon become a norm among leading pharmaceutical firms.
Digital Integration and Smart Packaging
Integration of data-tracking features within packaging systems is gaining traction. Rubber stoppers embedded with RFID or sensor technology can offer enhanced traceability and real-time monitoring, aligning with digital transformation in healthcare. These innovations can aid in cold chain monitoring, inventory tracking, and counterfeit prevention. With IoT applications becoming more common in medical logistics, demand for smart closures could create an entirely new product category. Advanced data-capturing stoppers can also enable predictive maintenance in supply chains.
Market Segmentation
Based on Product Type:
- Sleeve Stopper
- Straight Plug Stopper
- Snap On Stopper
- Conical Stopper
- 3Leg Stopper
Based on Application:
- Injection Stopper
- Infusion Stopper
- Lyophilization Stopper
- Pharmaceutical Disc
- IV Administration
Based on Material:
- Butyl Rubber
- Chlorobutyl
- Bromobutyl
- EPDM
- Natural Rubber
- Nitrile
- Silicon
Based on Coating:
- B2 Coating
- Flurotech & Teon Coating
Based on Sterilization Technology:
- Autoclavable
- Gamma Irradiation
Based on Diameter Size:
- 13mm
- 20mm
- 28mm
- 32mm
Based on End Use:
- Pharmaceutical
- Medical & Healthcare
- Chemical
- Research & Development
Based on Geography:
North America
- U.S.
- Canada
- Mexico
Europe
- UK
- France
- Germany
- Italy
- Spain
- Russia
- Belgium
- Netherlands
- Austria
- Sweden
- Poland
- Denmark
- Switzerland
- Rest of Europe
Asia Pacific
- China
- Japan
- South Korea
- India
- Thailand
- Indonesia
- Vietnam
- Malaysia
- Philippines
- Taiwan
- Rest of Asia Pacific
Latin America
- Brazil
- Argentina
- Peru
- Chile
- Colombia
- Rest of Latin America
Middle East & Africa
- GCC Countries
- South Africa
- Rest of the Middle East and Africa
Regional Analysis
North America holds a prominent position in the sterile rubber stopper market, primarily due to the presence of large-scale pharmaceutical manufacturers and strict regulatory compliance enforced by the U.S. FDA. The U.S. leads in biopharmaceutical production, boosting demand for sterile packaging. Canada also benefits from a well-established healthcare system, and Mexico is emerging as a nearshore hub for contract manufacturing. High per capita healthcare expenditure further supports ongoing innovation and adoption of premium-grade rubber closures.
In Europe, countries such as Germany, France, and the UK are witnessing stable growth, supported by investments in biologics and oncology drugs. Regulatory standards across the EU ensure consistent demand for high-quality rubber stoppers with superior sealing and sterility. Italy and Spain also play a key role in generic drug manufacturing. Moreover, pan-European initiatives to strengthen pandemic preparedness are leading to higher production volumes and packaging needs. The European Medicines Agency (EMA) mandates strict material compliance, boosting demand for validated solutions.
Asia Pacific is emerging as the fastest-growing region, driven by expanding healthcare infrastructure in China, India, and Japan. The region is a hub for contract manufacturing organizations (CMOs) and generic drug producers. Moreover, rising health awareness and government-backed vaccine initiatives contribute to rising consumption. Countries like South Korea, Indonesia, and Thailand are also scaling up local pharmaceutical capabilities. Increased investment in cold chain logistics and pharmaceutical exports is accelerating market penetration.
Latin America, though smaller in market share, is growing steadily. Brazil and Argentina lead the region, backed by pharmaceutical imports and increasing local production. The adoption of international quality standards is further supporting market development. Chile, Peru, and Colombia are opening new market avenues through trade agreements. In the Middle East & Africa region, the Gulf Cooperation Council (GCC) countries are investing in pharmaceutical manufacturing hubs. South Africa also exhibits growth, fueled by rising public healthcare expenditures and regional distribution centers. Overall, these regions together account for substantial future market share.
Top Companies
- RubberMill
- Saint-Gobain Performance Plastics
- Datwyler Holding Inc.
- Jiangsu Hualan New Pharmaceutical Material Co., Ltd.
- SABIC
- West Pharmaceutical Services, Inc.
- Shandong Pharmaceutical Glass Co., Ltd.
- Sumitomo Rubber Industries, Ltd.
- Ningbo Xingya Rubber & Plastic Co., Ltd.
- AptarGroup, Inc.
- DWK Life Sciences GmbH
- Daikyo Seiko, Ltd
Future Outlook
- Technological advancements in coating and sterilization will improve drug compatibility.
- Demand for prefilled syringes will boost sterile stopper applications.
- North America and Asia Pacific will continue to lead in innovation adoption.
- Sustainable and recyclable rubber materials will gain market share.
- CMOs will invest more in sterile packaging infrastructure.
- Automation in rubber stopper production will increase operational efficiency.
- Biologic drug pipelines will drive demand for specialized stoppers.
- Custom stopper sizes and designs will meet niche market needs.
- Growth in clinical trials will fuel demand for low-volume sterile packaging.
- Strategic partnerships between pharma and packaging firms will intensify.
Read more: https://www.credenceresearch.com/report/sterile-rubber-stopper-market